The Importance of Selecting the Right CNC Parts Manufacturer for Your Project
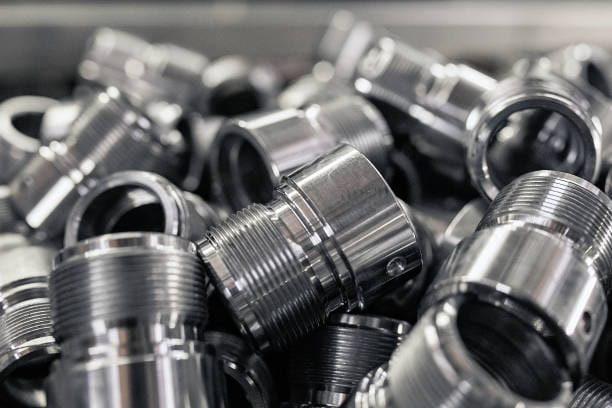
Choosing the right CNC parts manufacturer is key to the success of any project, especially in industries such as automotive, aerospace, and medicine that require custom precision parts. With so many contractors in the market, it’s easy to forget that not all of them will deliver the standards, quality, and deadlines set to ensure that your CNC milled parts are delivered on time. In truth, the entire production process of an item is optimization revolves around selecting the most suitable precision parts manufacturer. In this post, you will learn the most important aspects to keep in mind when choosing a CNC parts manufacturer, with emphasis on precision, reliability, and proficient customer care.
Understanding the Role of a Precision Parts Manufacturer
When it comes to creating components that need to adhere to specific requirements, a manufacturer helps in the production of such parts. They use state-of-the-art CNC (Computer numerical control) machines to manufacture parts with high precision. Computer generated images control the movement of the machine tools which means these machines cut, drill, mill, shape and do everything with precision. It enables the instruments to produce complex geometrical parts that can’t even be done with standard manufacturing techniques.
Aerospace, automotive, and electronics, for example, B2B companies need CNC technology all the time. It is essential to choose the right manufacturer so that the machinery produced is not only within the expected economic limits but also works as intended. From full-fledged production runs to prototype development, volume of the component does not matter with the right manufacturer. What does matter though is the expertise and machinery offered.
Picking a precision parts manufacturer that understands the need for quality in the particular sector comes with many benefits. With those provided comes a new significant competitive advantage. Their guidance in choosing the materials, component’s design, and even quality control guarantees achieving the expected performance of the sophisticated parts.
Lead Time and Delivery: Key Considerations
A business environment is fast-paced; hence the lead time and delivery schedule and selection of the CNC parts manufacturer are equally important. Components are often delivered too late and CNM milled parts are produced too slowly, which can cause expensive disruptions in the supply chain and significantly develop cost delays within a product. Timely delivery is critical to the success of any project and if it goes beyond the planned schedule, it may be a bit hard to achieve deadlines.
As a business, you are more likely to achieve smooth production processes if you choose high-quality CNC parts manufacturers that deliver in its promised timelines. A manufacturer with an ideal reputation takes full responsibility in being open with customers regarding delays and providing a comprehensive production plan with set guidelines and timelines. There should also always be the ability to urgently change the order quantity which enables a business to remain agile. Furthermore, manufacturers need to be kept at the loop on how production processes are progressing so that delivery can be done on time.
You should also check previous records of the manufacturer if they were able to successfully complete similar projects and if they met the timeline. It would be also beneficial if the provider includes communication around stemmed delays independent of them such as supply chains and predictive production scope limitations. Always delivering on time is vital in ensuring operations run smoothly as well as reducing the chances of any potential delays affecting your business.
Material Selection and Customization
Another key factor when selecting a CNC parts manufacturer is their ability to work with a variety of materials and offer customization options. Different industries require different materials for their CNC milled parts, and a precision parts manufacturer should be equipped to work with a wide range of metals, plastics, composites, and alloys.
For example, the aerospace industry often requires components made from high-strength alloys such as titanium or aluminum, while the medical device industry may need parts made from biocompatible materials like medical-grade stainless steel or plastics. The ability to customize parts based on the material and design specifications ensures that the components will perform as expected in the final product. Additionally, the manufacturer should be able to offer value-added services, such as surface treatments, coatings, and heat treatments, that enhance the performance of the parts.
The right manufacturer will also be able to provide advice on material properties, helping you choose the most suitable option for your application. They should be knowledgeable about the different material characteristics, such as strength, corrosion resistance, and thermal conductivity, ensuring that your CNC milled parts meet all technical requirements. Customization options can also extend to geometry, color, size, and finish, ensuring that your parts are tailored to meet your exact specifications.
Quality Assurance and Compliance with Industry Standards
Assuring quality comes next on the list of deciding factors when choosing a precision parts manufacturer. The field of manufacture, automotive, aerospace and medical industries, have products that undergo highly scrutinized standards and testing. A dependable manufacturer must guarantee that there is an active and constantly evolving quality control system for all CNC milled parts. They must undertake comprehensive inspection procedures, which are obstruction of dimensional, visual, and functional checks, to guarantee that the elements comply with set design and industry standards as well as the specifications.
Most well known precision parts manufacturers are already renowned for holding international quality standards as ISO 9001, therefore they conform to industry specific regulations. This also means they are certified to produce the parts with the required specifications because they follow quality control measures. These measures put in place are essential for businesses who operate in highly sensitive and complex industries.
Confirm that the manufacturer is willing to provide you with the relevant documents ensuring their claim of quality guarantees before you decide on a CNC parts manufacturer. Also what testing processes are in place, what standards are used during manufacturing and look into details. This will help you trust that the parts you will be supplied with will require no adjustments and can be used directly in your final product.
A supplier that possesses a robust quality control mechanism will eliminate discrepancies, cut down the expenses on rework, and ensure that the quality of products is uniform.
Conclusion
Choosing the right CNC parts manufacturer is quite essential as it can greatly influence the outcome of your project. The CNC parts manufacturer should always deliver value on time and with utmost precision. Be it CNC milled parts of sophisticated equipment, automotive parts, or even CNC parts for medical machinery, the manufacturer of choice must possess a good reputation and the capability to complete your project on time and with the required quality.
The shifts in leads and materials chosen, in addition to quality checks and customer care are all aspects that can help you make the decision while avoiding costly delays and unneeded mistakes. Within the domain of B2B manufacturing, having a trustworthy precision parts manufacturer enables you to achieve a great competitive position on the market while improving the outcome of your product development processes.
Also Read: Exploring the Capabilities of Gravure Printing Machines for Packaging Materials