The Future of Aluminum Sheet Fabrication in Automotive Design
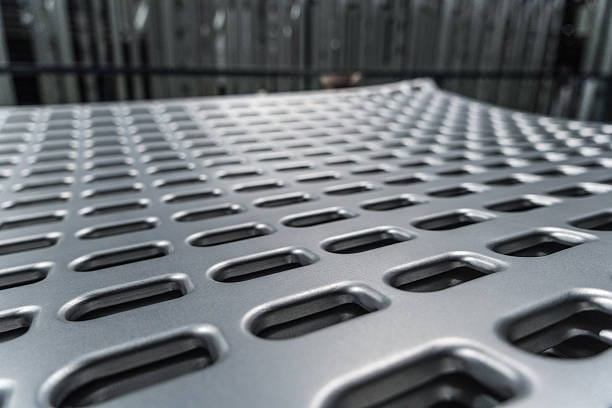
Aluminum is at the forefront of innovations in the automotive industry which focuses on reducing the weight of the vehicle with the use of advanced materials. Aluminum sheet fabrication technology makes it possible for auto manufacturers to easily comply with environmental policies by reducing the weight of vehicles and increasing fuel economy. There will be an increased supply of high-performance automotive aluminum parts due to advances in sheet metal fabrications.
This article analyzes the implications of these advancements on the automotive industry, considering the benefits and applications of aluminum sheet fabrication, as well as its overall impact on vehicle design. Increased fabrication capabilities of aluminum in the automotive industry should enable better utilization of the advantages of aluminum.
The Role of Aluminum in the Automotive Industry
Due to its lightweight nature, lack of corrosion, and strength, aluminum has for a long time remained a core material in the automotive industry. Advances in aluminum sheet fabrication have further increased its viability to automobile manufacturing. Considering manufacturer’s need to adhere to eco-friendly vehicle construction along with government fuel economy regulations, the practicality of aluminum metal in automobile construction continues to rise.
The use of aluminum is particularly helpful for automobile industries that wish to reduce the overall weight of the vehicles. The lighter the vehicle is, the less fuel it consumes and the lesser the emissions it produces, thereby aiding in achieving the sustainability goals of the industry. Focusing on electric vehicles (EVs), due to relying extensively on batteries, lightweight materials are essential to further improve battery efficiency and range.
Automotive grade aluminum parts can be more easily fabricated with the advent of precise aluminum laser cutting techniques. Furthermore, modern fabrication methods such as aluminum die casting allow the construction of stronger and lightweight body parts and even structural body parts.
Advancements in Aluminum Sheet Fabrication Techniques
The aluminum components utilized in the automotive industry are becoming more sophisticated, accurate, and affordable due to perpetual progress in technologies related to the fabrication of aluminum sheets. These developments aid in meeting the high demand for aluminum as well as the latest innovations in automobile engineering.
One of the greatest improvements is the fabrication of sheet metal parts which is now capable of dealing with thinner and stronger aluminum parts. The development of precision laser cutting, CNC bending, and stamping processes has brought improvements to fabrication accuracy which has opened new possibilities for complex and detailed parts. With this advancement, the use of aluminum parts is increasingly being adopted in vehicles. This incorporation improves the performance of the vehicle, while simultaneously decreasing the use of heavy materials such as steel.
Additionally, the complexity associated with enabling the fabrication of strong, lightweight aluminum parts that are capable of enduring everyday use has been mitigated greatly. This is extremely beneficial for body panels, bumpers and chassis where strength and weight are crucial components to the performance of the vehicle.
Applications of Aluminum in Automotive Design
The applications of aluminum sheet fabrication in automotive design are vast and growing. From body panels to structural elements, aluminum is increasingly being used in various parts of a vehicle due to its lightweight properties, strength, and ability to be shaped with high precision.
- Body Panels and Exterior Components: One of the most common uses of aluminum in automotive design is in body panels and exterior components. Sheet metal fabrications enable manufacturers to create large, complex panels that are both lightweight and strong. These panels improve fuel efficiency by reducing the overall weight of the vehicle while still providing the strength necessary to meet safety standards.
As automotive designs become more sophisticated, aluminum sheet fabrication offers flexibility in creating innovative shapes and contours that enhance both the aesthetic appeal and aerodynamic efficiency of vehicles.
- Structural Components: Aluminum is also used in structural components such as frames, chassis, and supports. These parts need to be incredibly strong while maintaining a low weight, which is where aluminum’s high strength-to-weight ratio comes into play. Advanced sheet metal fabrications ensure that aluminum can be used to create high-strength components without sacrificing the integrity or safety of the vehicle.
Using aluminum sheet fabrication for structural components also allows automakers to meet safety regulations while reducing vehicle weight. This is essential as the automotive industry continues to pursue fuel efficiency and sustainability goals.
- Heat Exchange and Cooling Systems: Another significant application of aluminum in automotive design is in heat exchange and cooling systems. Aluminum’s excellent thermal conductivity makes it an ideal material for creating radiators, intercoolers, and heat exchangers. These components help regulate the temperature of the engine and other critical systems, improving overall vehicle performance.
Through sheet metal fabrications, aluminum parts can be produced with precise designs that optimize heat dissipation, ensuring the cooling systems work efficiently while keeping the vehicle lightweight.
The Future of Aluminum Sheet Fabrication in Automotive Design
The future of vehicle designs considering aluminum sheet fabrication is promising due to constant improvements in technology and the need for lightweight, sustainable materials. As automakers invest in innovations, the use of aluminum in constructing new vehicles will be more pronounced.
Aluminum fabrication for the future does have some notable expected developments such as the creation of newer, lighter, and stronger alloys. The performance and the efficiency of aluminum components in vehicles will further improve which is great for the automotive industry. The advancements in alloys means manufacturers will easily incorporate them into a wide range of applications which will be facilitated by sheet metal fabrications.
Cost and precision is expected to greatly improve for aluminum sheet fabrication due to the progression of other manufacturing methods such as 3D printing as well automated welding. These methods will enable automakers to produce modern vehicles in lesser time and cost by crafting intricate and unique components tailored to specific requirements of contemporary vehicles.
Conclusion
The use of aluminum in car manufacturing will only increase with developments in aluminium sheet metal fabrication technology. Moreover, the automotive industry is moving to more eco-friendly practices which means deals and innovations in vehicle production would be of serious importance.
The cost of producing and maintaining vehicles is exponentially decreased due to the use of aluminum because it is lightweight while simultaneously increasing performance. These benefits, alongside booming demand for fuel-efficient vehicles, put aluminum sheet fabrication at the forefront of automotive design innovation.
Also Read: Mastermind Behind JD Engineering’s Automotive Excellence