The Evolution and Impact of Industrial Gas Turbines: Powering Progress
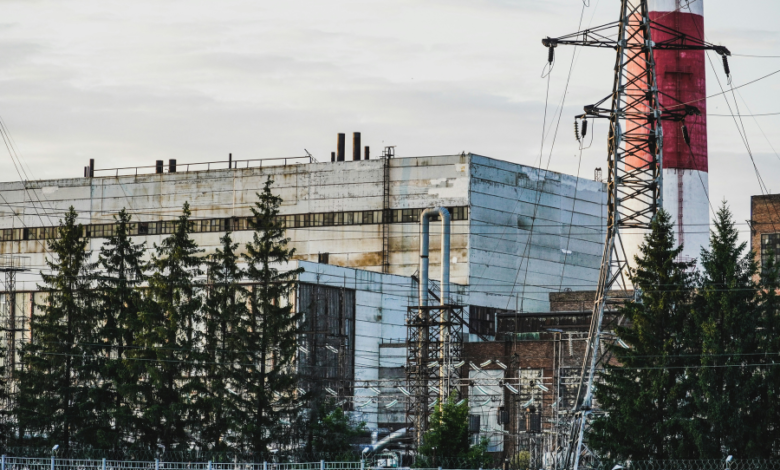
In the world of energy production and industrial applications, few inventions have had as significant an impact as the industrial gas turbine. These engineering marvels have revolutionized power generation, aviation, and various industrial processes. From their humble beginnings to the sophisticated machines of today, gas turbines represent a pinnacle of human ingenuity and innovation. This article delves into the history, workings, applications, and future of industrial gas turbines.
The Origins: Early Days of Gas Turbines
The concept of the gas turbine dates back to the 20th century when engineers sought more efficient ways to harness energy. While the principles of the gas turbine were understood, it was Sir Frank Whittle, a British engineer, who is often credited with creating the first practical design in the 1930s. Whittle’s pioneering work laid the foundation for the development of modern jet engines and industrial gas turbines.
How Gas Turbines Work
At their core, gas turbines operate on a simple principle: air is compressed, mixed with fuel, ignited, and then expanded to drive a turbine. This process is continuous, with incoming air providing the necessary oxygen for combustion. The resulting hot gases expand through a series of turbine blades, driving them and, in turn, producing mechanical energy.
Key Components of a Gas Turbine:
Compressor: The compressor section of a gas turbine is responsible for drawing in air and pressurizing it before entering the combustion chamber. This compression raises the air temperature, making it ideal for combustion.
Combustion Chamber: Here, fuel is injected and mixed with the compressed air. The mixture is then ignited, producing high-temperature, high-pressure gases.
Turbine: The hot gases from the combustion chamber flow through the turbine, where they expand rapidly, driving the turbine blades. This rotation generates mechanical energy used to power various applications, such as electricity generators or propulsion systems.
Exhaust: After passing through the turbine, the exhaust gases exit the system. In some designs, these gases can be harnessed for additional purposes, such as heating or combined with steam to drive a steam turbine for increased efficiency (known as combined cycle power plants).
Applications Across Industries
Power Generation
One of the primary applications of industrial gas turbines is power generation. Gas turbines are used in both standalone power plants and as part of combined cycle power plants. In a combined cycle setup, the waste heat from the gas turbine is used to produce steam, which then drives a steam turbine, significantly increasing overall efficiency.
Aviation
Gas turbines revolutionized the aviation industry, enabling aircraft to travel faster, farther, and more efficiently. Jet engines, a type of gas turbine, power most commercial and military aircraft today. Their high power-to-weight ratio and reliability have made air travel accessible to millions worldwide.
Oil and Gas Industry
In the oil and gas sector, gas turbines play a crucial role in various processes. They drive compressors for natural gas pipelines, provide power for offshore platforms, and are used in refineries for process heat and electricity generation.
Marine Propulsion
Gas turbines are favored for marine propulsion due to their compact size, high power output, and quick start-up capabilities. They are often used in naval ships and high-speed vessels where space and speed are critical factors.
Industrial Applications
Beyond these major industries, gas turbines find use in diverse industrial applications. They provide reliable power for factories, hospitals, data centers, and other facilities where a continuous and stable power supply is essential.
Advantages of Gas Turbines
Efficiency
Gas turbines boast high efficiency, especially in combined cycle configurations. Their ability to utilize waste heat for additional power generation makes them a compelling choice for electricity producers looking to maximize efficiency.
Flexibility
Gas turbines can start and stop quickly, making them ideal for meeting fluctuating energy demands. This flexibility allows power plants to respond rapidly to changes in electricity needs, such as during peak demand periods or to balance renewable energy sources’ intermittency.
Low Emissions
Modern gas turbines are designed to produce lower emissions compared to traditional fossil fuel power plants. Advanced combustion technologies and stringent environmental standards have led to significant reductions in nitrogen oxides (NOx), sulfur dioxide (SO2), and particulate matter emissions.
Reliability
Gas turbines are known for their reliability and long operational life. With proper maintenance, they can operate for thousands of hours, providing a stable power supply for critical applications.
Challenges and Future Developments
Emissions Reduction
While gas turbines have made strides in reducing emissions, the industry continues to focus on further improvements. Research is ongoing to develop cleaner combustion technologies and explore alternative fuels such as hydrogen, biofuels, and synthetic fuels.
Efficiency Improvements
Engineers are constantly working to enhance gas turbine efficiency, aiming to squeeze more power from each unit of fuel. Advanced materials, improved aerodynamics, and better control systems all contribute to incremental efficiency gains.
Integration with Renewable Energy
Gas turbines are increasingly being used in conjunction with renewable energy sources like solar and wind. These hybrid power plants provide a stable energy supply, addressing the intermittency issues inherent in renewables.
Digitalization and Predictive Maintenance
The rise of digital technologies enables real-time monitoring of gas turbines. Data analytics and predictive maintenance algorithms can anticipate and prevent failures, reducing downtime and optimizing maintenance schedules.
Conclusion
The industrial gas turbine stands as a testament to human innovation and engineering prowess. From its beginnings as a concept to its ubiquitous presence in power generation, aviation, and industry, the gas turbine has shaped the modern world. With a focus on efficiency, reliability, and environmental responsibility, the future of gas turbines looks promising. As technology continues to evolve, these turbines will play a vital role in our quest for cleaner, more sustainable energy solutions. Whether propelling aircraft through the sky or lighting up cities, the industrial gas turbine remains a powerhouse of innovation, driving progress in countless ways.